OEM Project Team Designs, Builds, and Races Electric Car in Just One School Year
During the 2024-25 season, OEM project team members set a bold goal: to design and build a fully functional electric car within one academic year, racing it at the annual SAE Student competition in June - a task that hasn't been done in 8 years. It was a massive and exciting challenge, full of wild ups and downs. In the end they accomplished something extraordinary.
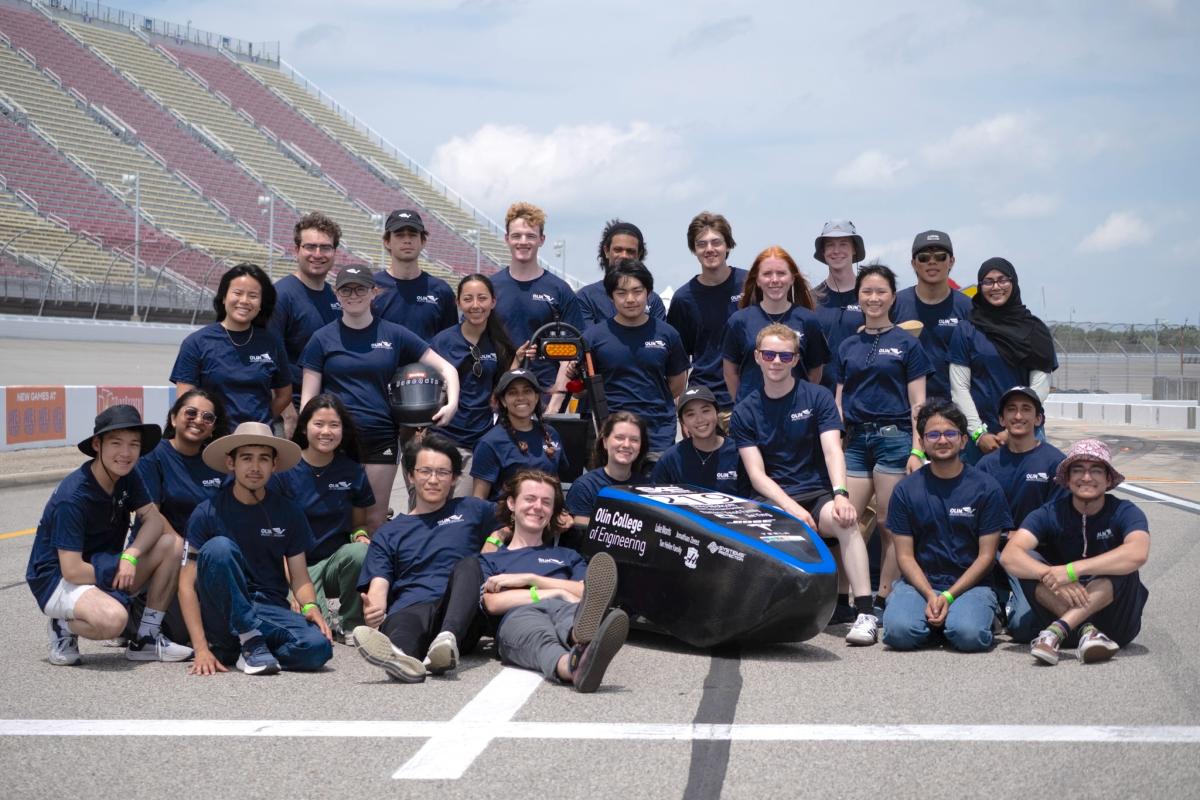
Olin Electric Motorsports (OEM) at the Michigan International Speedway for the 2025 Formula SAE Student competition in Detroit, MI. For the first time in eight years and four car generations OEM built a fully functional racecar in a single academic year.
Wired for Collaboration
Olin Electric Motorsports (OEM) is an undergraduate project team at Olin focused on educating student engineers through developing and manufacturing electric race cars. Electric vehicles provide a platform for the team to pursue in-depth mechanical, electrical, computer, and systems engineering.
By working together—much like the 50 interconnected circuit boards in their current car, Mk VII, which must communicate and function reliably to keep the driver, team, and vehicle safe—OEM members develop not only technical knowledge, but also the communication and leadership skills essential to success as professional engineers.
Plus, with the team independently funded and Olin's hands-on approach emphasized throughout the academic experience, opportunities for student camaraderie, collaboration, and connecting classroom learning to real-world design and manufacturing projects, is abundant.
Not to mention having the chance to accomplish something that hasn't been done in almost a decade.
The Olin academic experience
Discover our Engineering Programs
Racing the Clock
"It was really a strategy game more than anything else," says Meagan Lipsman '26, project manager from the 24-25 season, when asked what made this academic year different from the previous eight.
"We very intentionally chose to scope the amount of work based on the one-year cycle. In everything we designed, we thought about Design for Manufacturing (DFM), reliability, and how we could decrease timeline risk as much as possible," says Lipsman.
The rule instituted by the students for the year was "only 30% of the car could change." "This constraint kept us from falling behind on timelines and over-scoping the car to the point where we could not finish it in one year," says first-year student Jake Hamilton '28, OEM project manager for the 25-26 season.
Having first-years and sophomores on the team (each year), as well as experienced juniors and seniors with everyone each having their own roles to play, contributed to this special year.
"Team management worked overtime to make sure everyone was receiving the support they needed, such as educational resources and design reviews from senior engineers. They were always there to support us with anything from feeling stuck to assembling a part on the car. Overall, the laser focus of the team and supportive management allowed us to accomplish what we had thought was near impossible!" adds Hamilton.
The team also employed a savvy tactic to reduce timeline risk, concentrating upfront on integrating and testing their electrical systems while first removed from the car, so that they could work in parallel.
"This allowed us to not be stalled by the car not being ready mechanically; we could still go ahead and do all the electrical testing," says Lipsman.
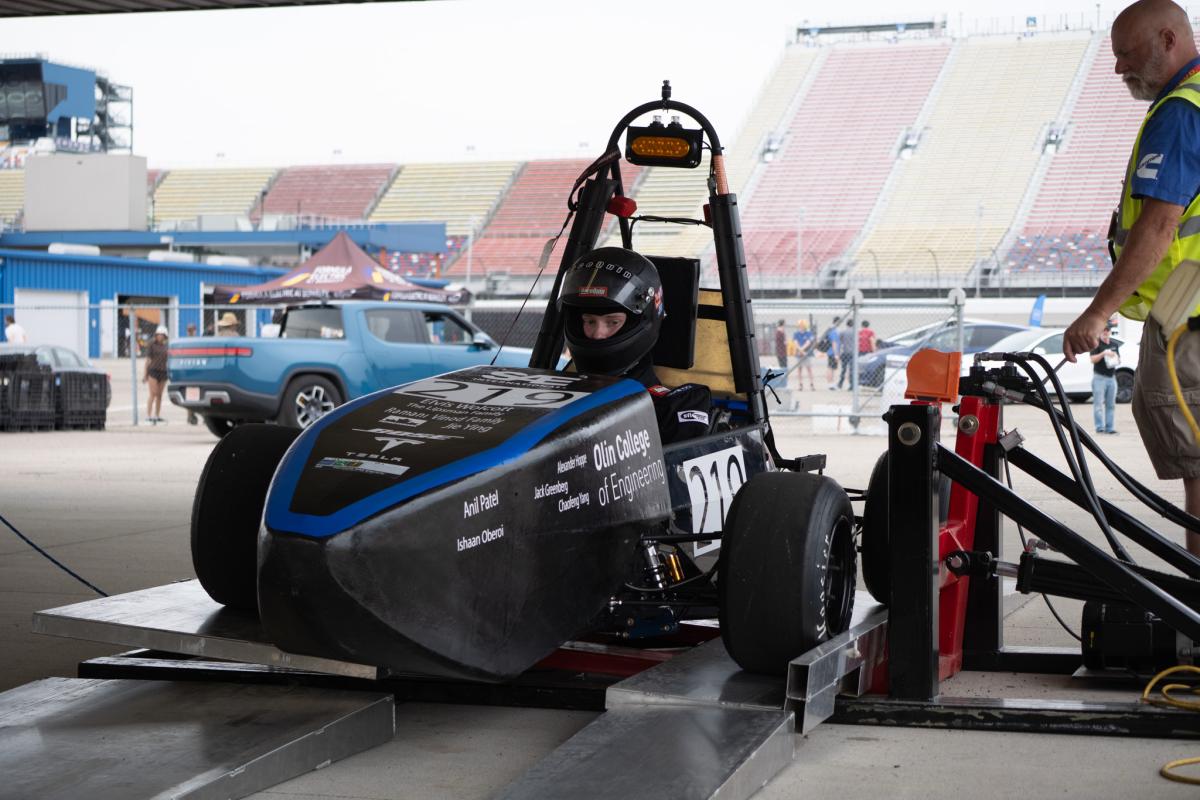
Jake Hamilton '28, OEM project manager for the 25-26 season, is shown inside MK VII during the tilt test at the June 2025 SAE Student Competition.
While on the mechanical side, the team integrated everything this past spring like the drivetrain, suspension, accumulator (battery), steering, and brakes. Having the clear goals, and "making sure everything was designed having 'good engineering practices'," was instrumental in making the feat possible, says Hamilton.
Lipsman agrees, saying "the goal was that at any point everyone should know exactly what their role was in moving forward and what the next big milestone was that we needed to hit to be done by the end of the year."
The team say they learned a lot while working to achieve these individual milestones and working toward the epic goal of not only designing and building a functional race car in just two semesters, but to also get it across the finish line - a series of tests faced by 100's of Oliners over the years where anything can go wrong to derail the mission.
Even a small leak.
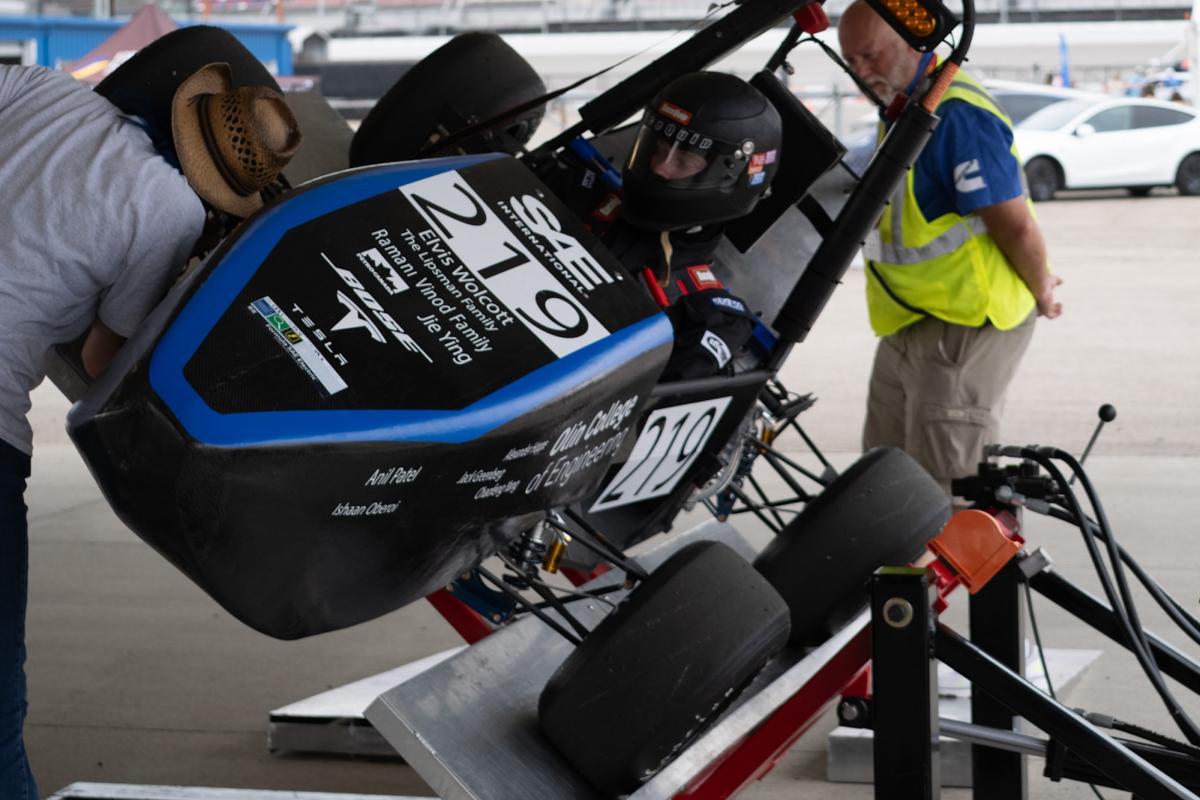
OEM’s MK VII car is seen doing the tilt test where the car is tilted 60 degrees from horizontal with a driver inside to make sure the car’s center of gravity is low enough to prevent the car from rolling. Driving the car is Jake Hamilton '28, project manager for the 2025-2026 competition season.
Back on Track
At the SAE Competition in Michigan this past June, the team faced an unexpected challenge. Mk VII wasn't able to race during the dynamic events because of a tiny leak into their main battery discovered during the competition rain test.
The first part of the competition each year is a series of technical inspections where judges put every element of a car under a microscope and make sure all safety standards are met. Only around 60% of teams pass these inspections because of the difficulty - the Oliners were in that 60%.
The tilt, rain, and brakes test was next. The tilt test involves tilting the car to 60 degrees and ensuring no fluids leak out and the car doesn’t tip over. The rain test involves spraying the car with water for 2 minutes and ensuring nothing fails. This is the test that tripped them up. But not for long.
"The whole team came together to support and help the effort of debugging, disassembling, and then attempting to fix the car after the leak was found. We had people as runners to get tools, we had the electrical members diagnosing circuit board issues, accumulator members drying and repairing the battery, and we even had members who weren’t at the comp on the phone to help us. It was truly an inspiring moment of camaraderie and perseverance," says Hamilton.
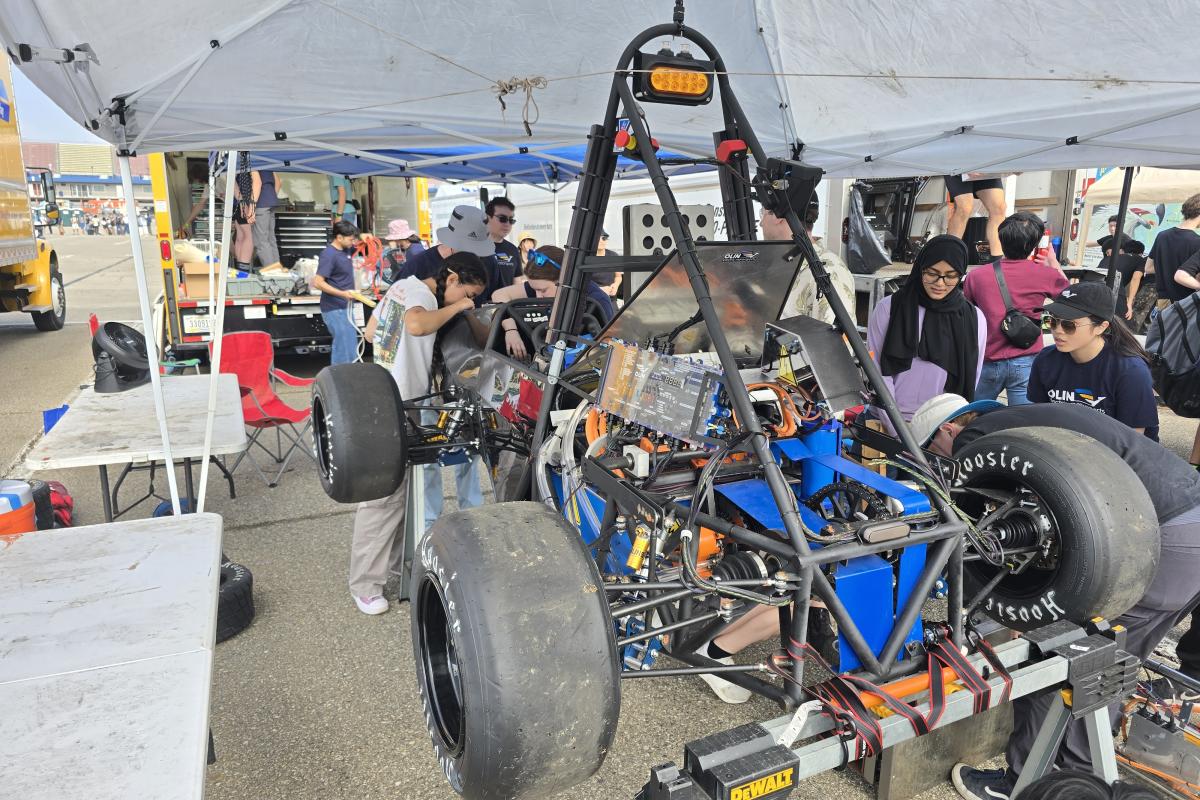
The OEM team members work on Mk VII during the SAE Competition in June 2025.
At the end of the day, the team accomplished their primary goal of building a electric race car in just one academic year, and they all "learned an incredible amount in the process, regardless if it drove in Michigan or not," says Lipsman.
"I remember saying "No matter what, Mk VII will drive again," and it did."
Not to be deterred, the Oliners traveled to Hampden County on July 15 for a drive day at Palmer Motorsports - thereby completing their racing objective.
Even though the race is now over and the team accomplished their bold goal, Mk VII doesn’t get to retire just yet, says Hamilton.
"We want to use the Mk VII as a test mule for sensors and data collection. Our plan is to do multiple drive days for Mk VII to collect more data on how much energy it used given a certain distance, what driving dynamics need to be changed, and a million other small data points to help us make informed design decisions for what's next - Mk VIII."
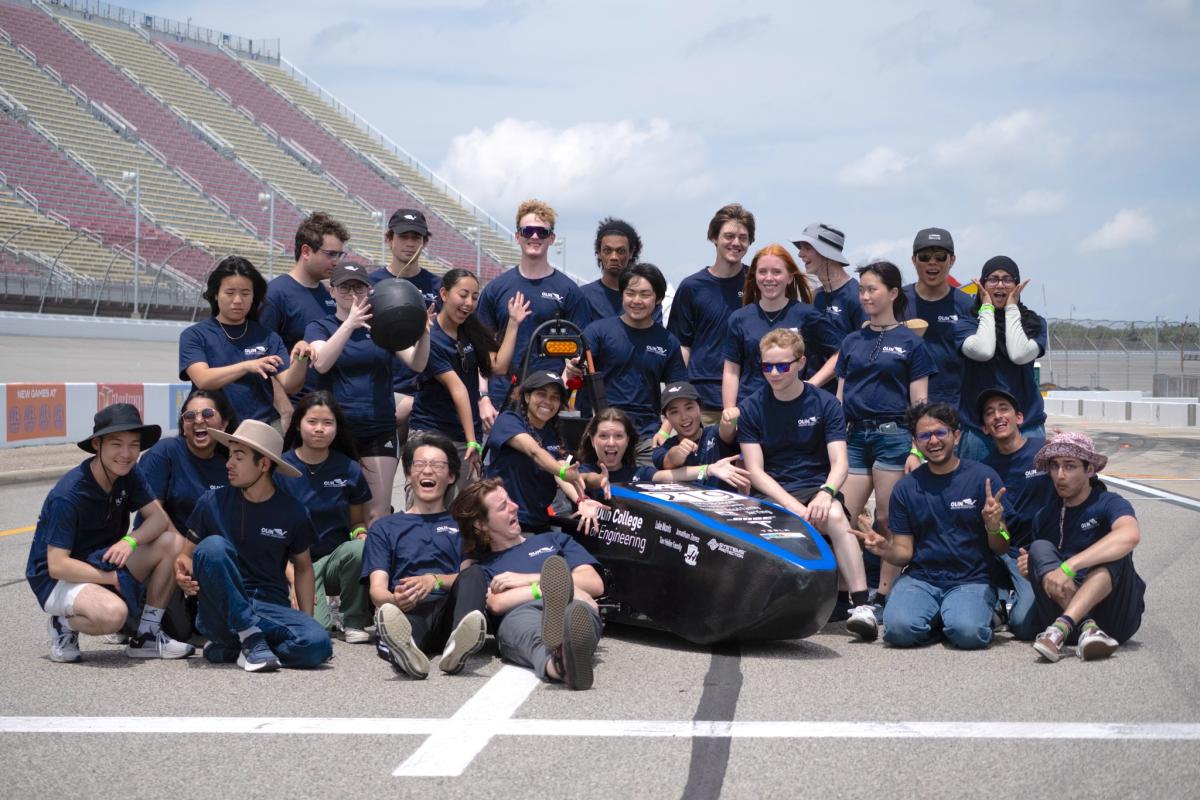
The Olin Electric Motorsports team take a fun group photo with their car at the Formula SAE Electric competition in 2024.